In Bangladesh, cement is the backbone of infrastructure development. It includes bridges, highways, power plants, urban expansion, and many more.
As the country moves forward with mega projects and industrialization, the cement sector plays a crucial role in it. Since independence till now, it has played a vital role in shaping the country’s future.
At Tiger Cement, we are proud to contribute to the development of the nation. In this guide, we take a deep dive into the cement production ecosystem of Bangladesh.
The Cement Industry in Bangladesh: An Overview
In the past two decades, the cement industry has experienced remarkable growth. At the beginning, it started as a fully import-dependent sector. As of right now, the sector is self-sufficient with over 35 operational cement companies.
The total installed production capacity exceeds 80 million metric tons (MT) annually. Whereas the domestic consumption remains around 35 million metric tons (MT). It highlights a significant overcapacity in the market (Mordor Intelligence, The Daily Star).
To compete in such a competitive market, all companies need to be evolving.
At Tiger Cement, we have responded to this change by adopting cutting-edge manufacturing practices. Also, focusing on delivering consistently high-quality cement that meets the local and international standard.
The Cement Manufacturing Process
Raw Material Preparation
A bag of cement consists of several materials. It includes limestones, clay, gypsum, fly ash, slag, and additives. However, Bangladesh lacks sufficient high-quality limestone reserves. As a result, it makes clinker (a key intermediate product) heavily import-dependent.
The first step of the process is to blend the imported clinker with locally sourced gypsum and additives. These are tested in our in-house labs to calculate chemical balance and uniformity.
Grinding and Blending
At Tiger Cement, we house the largest ball mill in the country. It has an annual production capacity of 1.512 million MT. At this stage, the clinker is ground with gypsum and additives to create a uniform cement blend.
The process is strengthened by our 4th generation High Efficiency Classifier (HEC). It ensures only properly sized particles exit the mill.
Later, the rough particles are recirculated for further grinding. This entire system and process help to reduce power usage for cement production. Also, it marks a milestone for energy efficiency in the country’s cement industry.
Pre-Heating and Pre-Calcining
Before clinker formation, the raw undergoes pre-heating. It involves a multi-stage cyclone system followed by pre-calcining. This step uses the waste heat and kiln exhaust gases to remove moisture. Furthermore, partially disintegrate limestone. Therefore, improving thermal efficiency and reducing energy usage in the kiln.
Clinker Formation in the Kiln
The pre-calcined material enters the rotary kiln; the heat is around 1,450 degrees Celsius. At this temperature, chemical reactions take place. It transforms the feed mix into hard grey nodules known as clinker, an essential intermediate in cement.
Cooling Process
The newly formed clinker exits the kiln at a very high temperature. Also, it is rapidly cooled using grate coolers. This quick cooling stabilizes mineral structures. At the same time, it improves the strength potential and recovers heat for reuse in the system.
Clinker Grinding
Later, the cooled clinker is mixed with gypsum and performance-enhancing additives. It is finely ground in our ball with a High Efficiency Classifier (HEC) to produce the final product, known as Tiger Cement.
Packaging and Distribution
The finished cement is packed in durable polypropylene bags. Afterwards, it is shipped in bulk via our distribution network across the country.
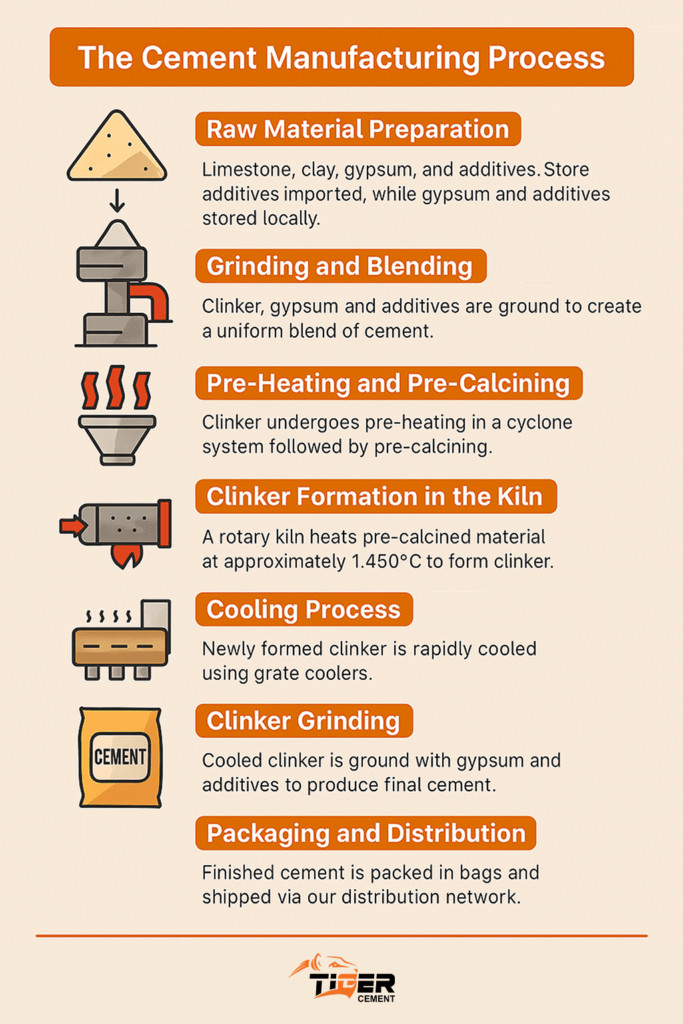
Challenges in Cement Production
Overcapacity
As mentioned earlier, the production capacity for cement is excess in relation to demand. As a result, it leads to price wars and pressure on margins for all the companies to compete (Daily Star).
Energy Costs
The cement manufacturing accounts for 2.9% of national energy use. Also, the fuel price fluctuations can directly impact the operational costs related to production (The Green Page, 2023).
Environmental Pressure
Cement contributes to nearly 1.5 million tons of carbon dioxide emissions annually in Bangladesh (CEIC Data, 2023). In recent years, the market has been shifting towards PCC. In comparison to OPC, it involves a more environmentally friendly manufacturing process.
Port Congestion
At times, port congestion can be an issue for cement production. Mongla and Chittagong port delays can affect the clinker import timelines and cost. As a result, affecting the overall timeline for the construction projects.
Dollar Rate
For cement production, 80% of the clinker is imported in Bangladesh. As a result, the dollar rate can have an effect on deciding the final price for the product. In recent years, the dollar rate has skyrocketed from 84 Tk to 121 Tk for $1 (XE).
For cement companies, the import of clinker has become more expensive for production. In the end, the price per bag has increased for retailers and contractors to purchase.
Sustainability and Innovation in the Cement Industry
Energy Efficiency as a Foundation
At Tiger Cement, we have invested in Vertical Roller Mills (VRMs) and ball mills with 4th Generation High Efficiency Classifiers (HEC). It helps to reduce the energy usage by up to thirty percent (The Daily Star). These systems improve productivity and lower emissions.
Emission Reduction and Environmental Controls
We control particulate and CO₂ emissions using:
- Electrostatic precipitators and bag filters
- Closed-loop water systems
- Real-time environmental monitoring
Alternative Fuels and Raw Materials (AFR)
We’re exploring:
- Refuse-Derived Fuel (RDF) as a partial coal substitute (IPEN, 2023)
- Blended cements with fly ash, slag, and pozzolanic materials
- Reduced clinker factor formulas
At Tiger Cement, we align with SDGs (Global Sustainability Alignment) 9, 12, and 13. Also follow the GCCA principles for climate-conscious cement production.
Waste Heat Recovery and Smart Manufacturing
To stay at the forefront of the industry, we are evaluating Waste Heat Recovery (WHR). Also, in discussion to integrate Industry 4.0 technologies. It includes IoT sensors, AI (artificial intelligence) for process optimization, and predictive maintenance systems.
Future Outlook
The industry is expected to grow from $4.47B in 2022 to $5.34B by 2027, a CAGR rate of 3.6% (Mordor Intelligence).
Currently, there are several megaprojects underway and many more to follow soon. At the same time, we are discovering opportunities for exporting our cement product to foreign countries.
Nonetheless, Tiger Cement is ready to scale with the nation’s ambitions.